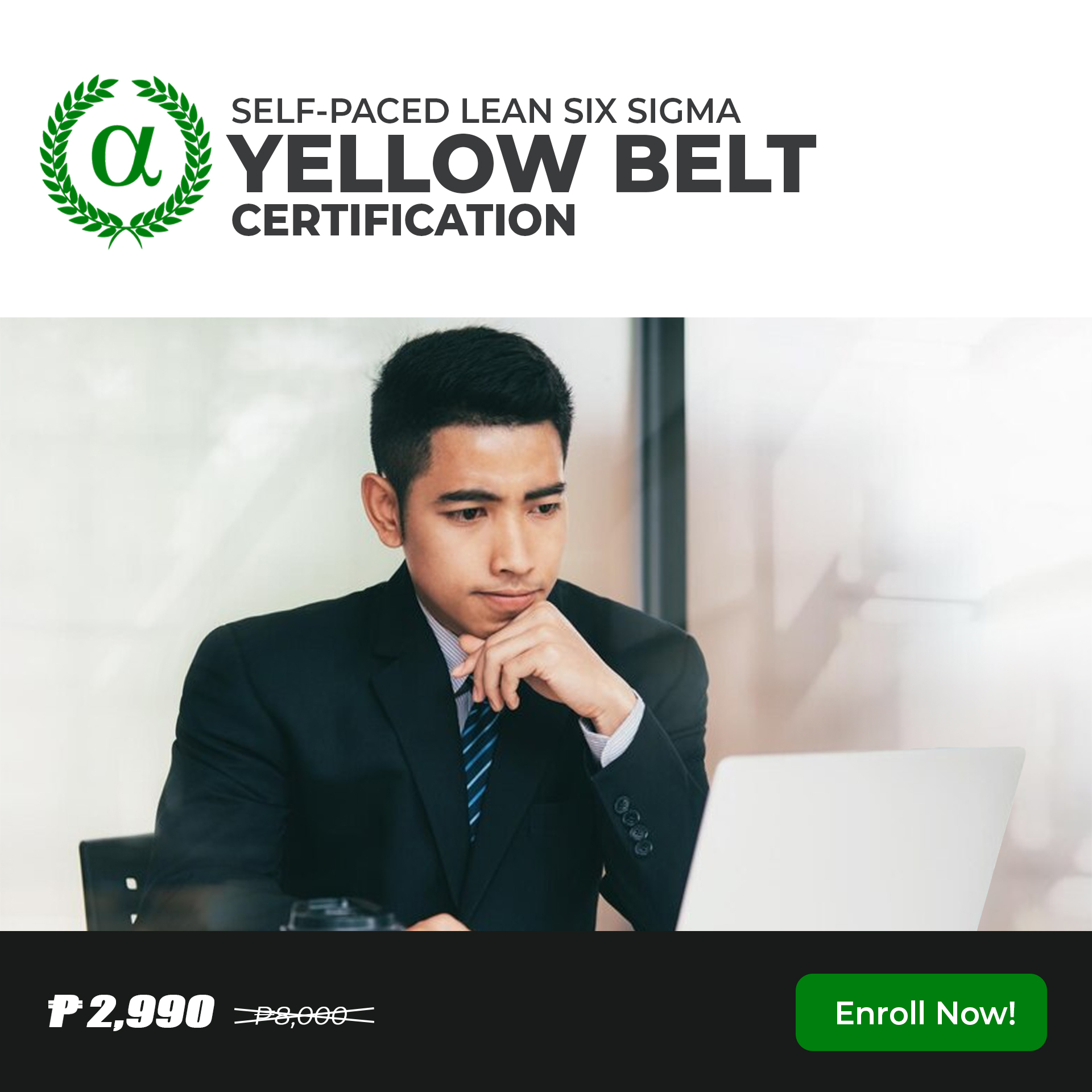
Lean Six Sigma Yellow Belt Certification
AL
Be #significantlybetter with our Internationally Accredited and Recognized Online Lean Six Sigma Yellow Belt Workshop and Certification Program!
Be #significantlybetter with our Internationally Accredited and Recognized Online Lean Six Sigma Yellow Belt Workshop and Certification Program! ?
About the Program
Yellow Belt is the entry-level to the Lean Six Sigma practice. Basic diagnostic and quality tools and techniques are taught in this program. The role of a Yellow Belt is highly focused on delivering localized improvements keeping in mind that such Lean Six Sigma projects must be operationally scaled in scope and depth to fit within their work area.
Program Rationale
Participants will learn the fundamental principles and thought processes of Lean Six Sigma leading to identifying and defining the right problem / opportunity, measuring the current process performance using the right data, validating the right root causes using data, improving using the right solutions and sustaining the gains using the right control measures.
Target Participants
All levels of employees from staff to executives who want to learn the Lean Six Sigma way of solving problems and improving processes.
Certification Requirements
✔ Completion of e-learning module + exercises + quizzes
✔ Pass the 50 item multiple choice, online proctored Internationally Accredited Certification Examination with at least 70% mark
✔ Demonstration of proficiency through the simulated case study using the Lean Six Sigma tools & techniques and Minitab
Program Outline
The program is crafted by leading Lean Six Sigma practitioners in the Philippines aligned with the Council for Six Sigma Certifications (CSSC) and American Society for Quality (ASQ) Body of Knowledge (BOK).
I. Introduction of ALPHA & the Internationally Accredited Lean Six Sigma Yellow Belt Program
a. Company and Program Introduction
b. Program Objectives, Outline, and Key Result Areas
c. How to Use this e-learning Module
II. Introduction to Lean Six Sigma
a. What is Lean Six Sigma?
b. Pillars of Lean
c. DOWNTIME - The Eight Wastes of Lean
d. Y = f(x) of Six Sigma Thinking
e. Lean Six Sigma Roles and Responsibilities
f. The Benefits of Applying Lean Six Sigma
g. DMAIC Roadmap
h. Companies Using Lean Six Sigma
III. Introduction to Digital Project - FeVer Beverages
IV. Define Phase
a. Define Phase Goals and Deliverables
b. Problem Solving vs Improvement
c. Choosing the Right Problem
d. Project Charter and Its Elements
e. How to Write an Effective Problem and Goal Statement
f. SIPOC Diagram for Project Scoping
g. Best Practices in Completing the Define Phase Deliverables
V. Measure Phase
a. Measurement Phase Goals and Deliverables
b. Process Mapping
c. Data in Lean Six Sigma
d. Data Types
e. Measurement Scales
f. Data Collection Plan
g. Statistics for Lean Six Sigma
h. Accuracy vs Precision
i. Introduction to Minitab
j. Basic Statistics Using Minitab
k. Measurement Systems Analysis - Is Your Data Source Reliable?
l. Best Practices in Completing the Measure Phase Deliverables
VI. Analyze Phase
a. Analyze Phase Goals and Deliverables
b. Brainstorming
c. Why - Why Analysis
d. Fish Bone Analysis
e. Graphical Analysis Tools
f. Tools for Data Distribution
g. Histogram
h. Boxplot
i. Pareto Chart
j. Tools for Tracking Data Over Time
k. Time Series Analysis
l. Tools for Checking Relationship Between Variables
m. Scatterplot
n. Think Outside the Box...plot!
o. Validation Table
p. Best Practices in Completing the Analyze Phase Deliverables
VII. Improve Phase
a. Improve Phase Goals and Deliverables
b. Commonly Used Lean Six Sigma Tools to Improve Processes
c. 5S for Workplace Productivity
d. Cross Training to Help Reduce Bottleneck Processes
e. Single Minute Exchange of Die (SMED) aka Pit Stop Concept
f. Visual Management
g. Standard Work
h. Mistake Proofing
i. PICK Matrix
j. Implementation Plan
k. Tools for Evaluation of Results
l. Best Practices in Completing the Improve Phase Deliverables
VIII. Control Phase
a. Control Phase Goals and Deliverables
b. Process Control Plan
c. Control Charts
d. Test for Special Causes of Variation
e. How to Select the Right Control Chart
f. Best Practices in Completing the Control Phase Deliverables
IX. Digital Project Submission
X. Certification Examination
XI. Conferment of Certification
Program Feedback and Reviews ⭐⭐⭐⭐⭐
“In just a short period of time, I have learned so many things about lean six sigma that can be helpful in managing and handling different projects and situations that can be solved in different ways. Furthermore, on how to present and implement various solutions to team members. Lastly, I would like to extend my gratitude to Sir Lex and his team for their passion in sharing their knowledge in Lean Six Sigma.” – Nell J. Penamante, Project Manager at Fibercom Telecom Philippines
“I have gained a deeper knowledge and understanding of what LSS really is since we do not have this particular course subject way back college. Especially the LSS tools in which I can apply in my workplace for process improvement. Also the knowledge and application of the course in MiniTab gives me an advantage for data analysis and later on to associate in my future business presentations!” – Charmaine C. Fortifaes, Project Coordinator at ALEC Dubai
“The program gave me a wider scope and more detailed elaboration of the DMAIC technique. I have already taken a LSSYB workshop and I think is better and more helpful. Also, I could relate all of the IE subjects and even my internship experience along the way!” – Thrizha-Anne D. Caampued, Wave 1 Valedictorian
“I like the content of this program considering it is online. It equipped me with a lot of knowledge as if in an actual class. It refresh my ideas on lean six sigma and how it is practiced.” – Justine Roy Balinado, Service Advisor at Toyota Dasmariñas, Cavite
“I was able to gain more knowledge about the Lean Six Sigma that was initially taught during college. It gives me the ability to improve the current process we have at work and also to sustain quality improvement. I also realized that this program will serve as a career advancement for me which I can apply across different industries.” – Faye Caryl R. Chico, Associate at Shell Business Operations
“I learned how to properly use the DMAIC methodology in process improvement. The video lectures are great. Short but very informative.” – Adrian L. Rey, Project Manager at Island Light and Water Energy Development Corp.
Learning Investment
Your learning investment includes access to our e-learning module, LSS tools & templates, examination fee, certification fee, e – certificate, access to our Alumni Network, and access to FREE learning sessions in this platform.
I have absolutely loved this course. The lessons are small enough that I can easily get at least one or two completed every day while being packed with valuable information. I'll definitely be taking more!
I had the best experience in online learning as the coaches knows the topic very well and they explained it so we can understand the topic as easy as possible. Had a good time. Thank you so much! :)
Overall, it was a good course on the basic foundation of Lean Six Sigma tools and how and when to use them
The program allowed me to further understand the Six Sigma principles and provide coursework that tests my ability to apply them to improve processes.
The Lean Six Sigma Yellow Belt Certification Program is perfect for busy individuals who wanted to upskill. I highly recommend this program to every one
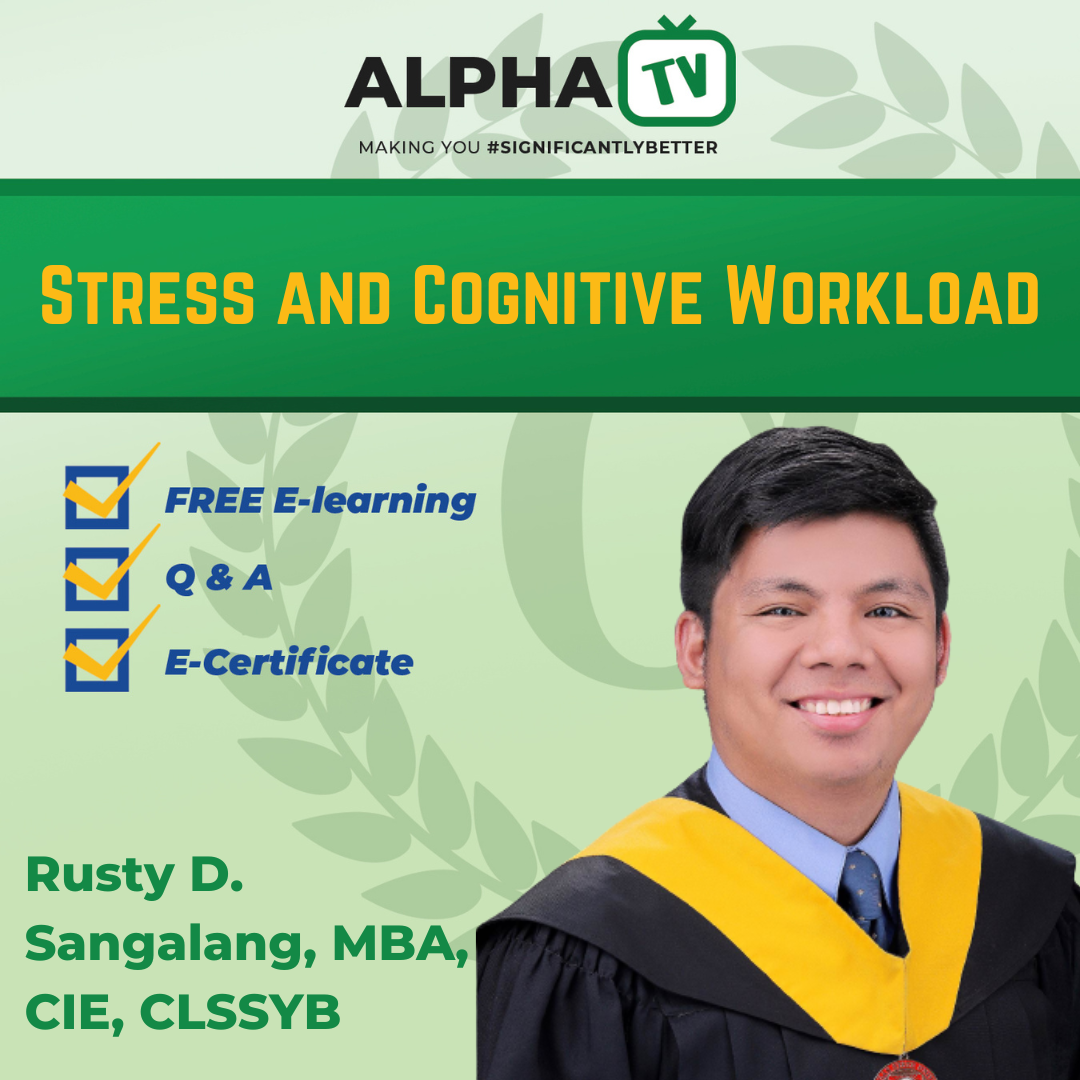
RS
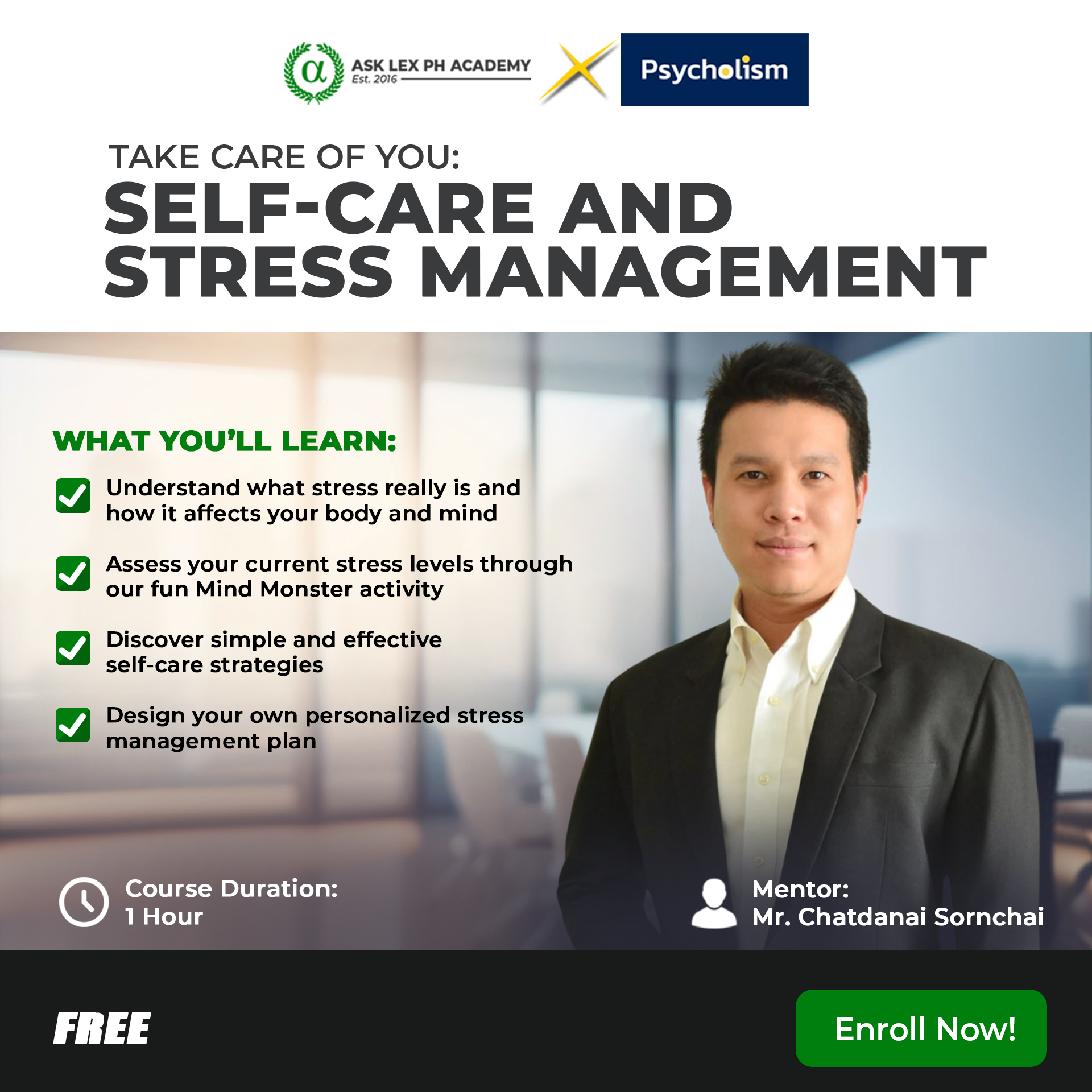
TP
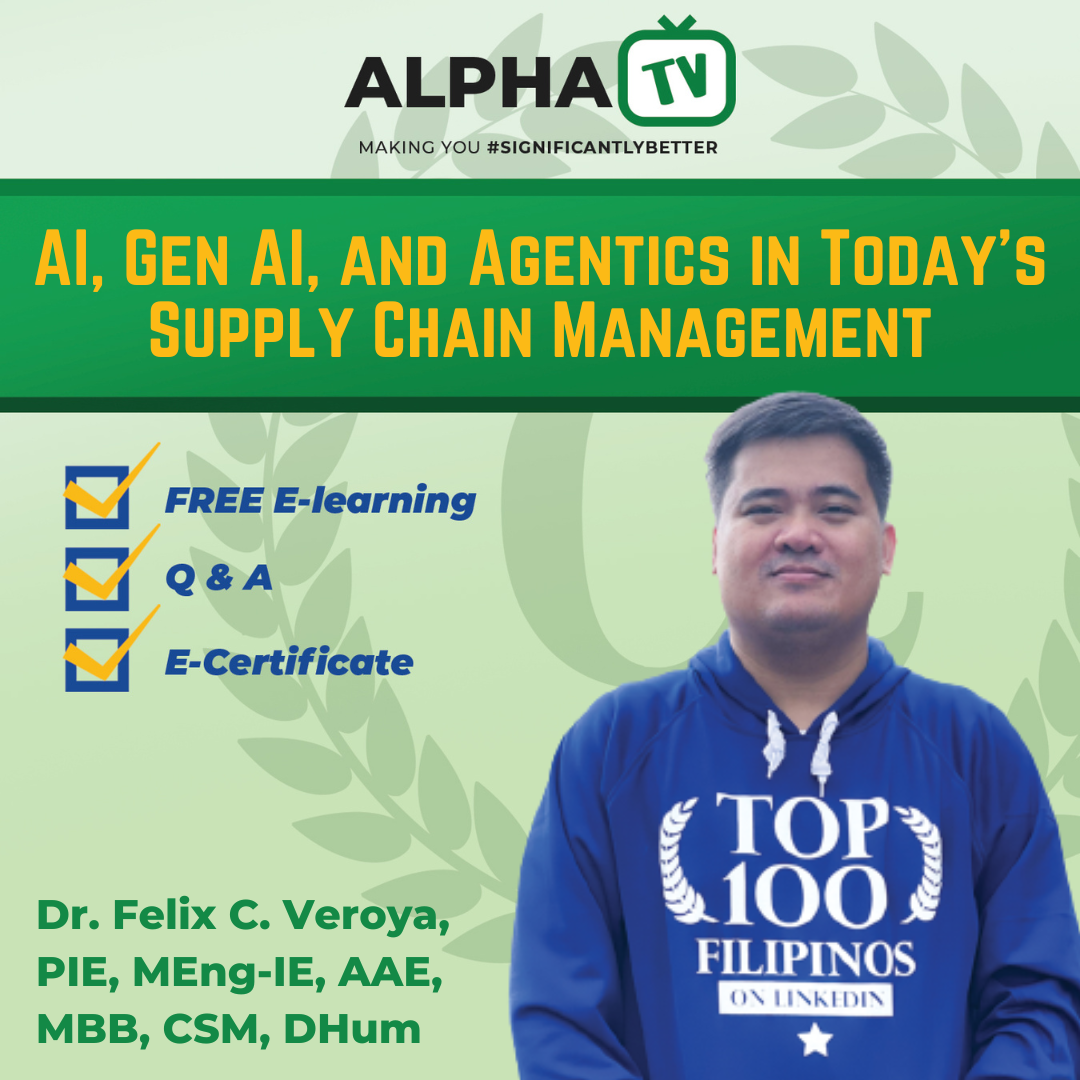
FV