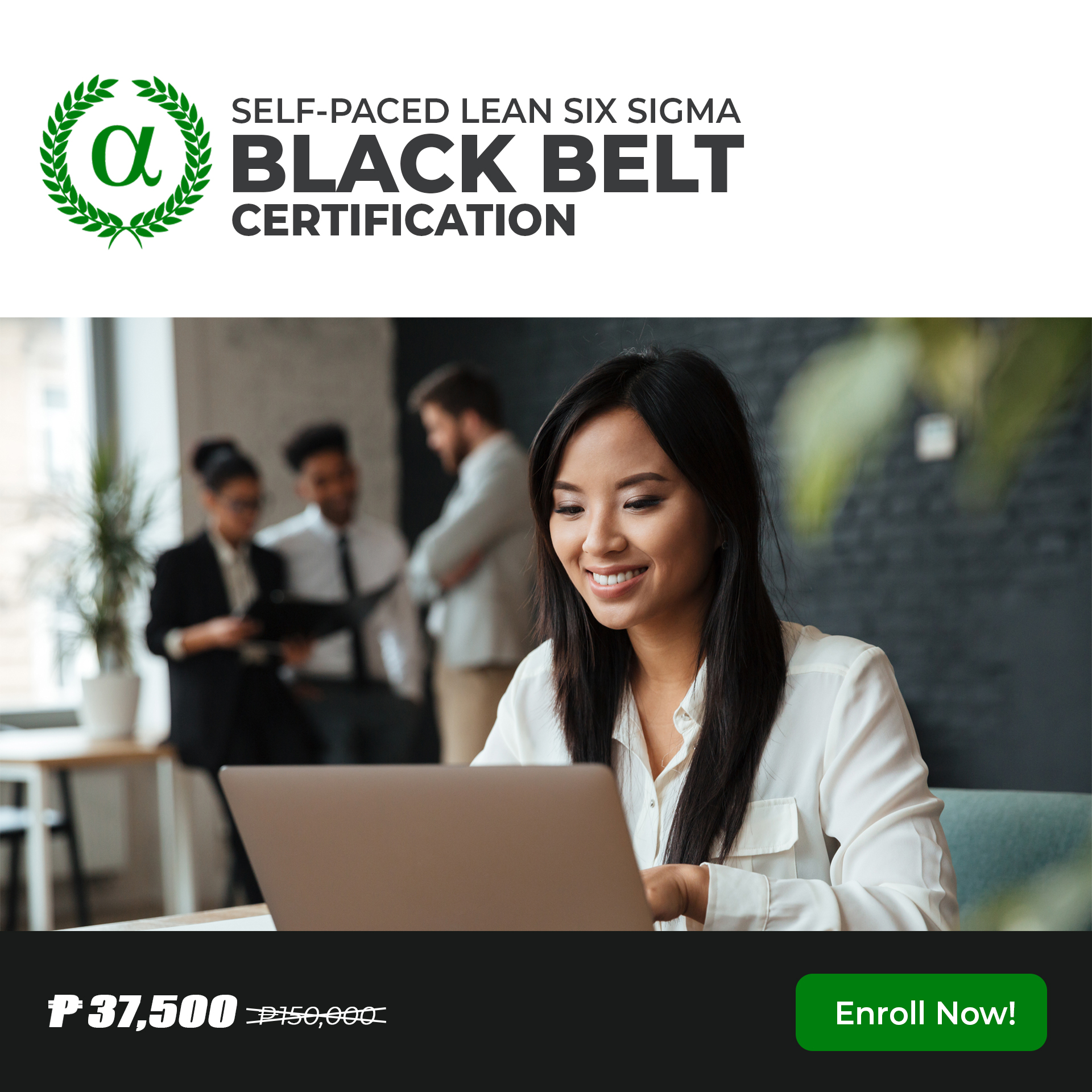
Who is a Lean Six Sigma Black Belt?
The Certified Six Sigma Black Belt (CSSBB) is a professional who can explain Six Sigma philosophies and principles, including supporting systems and tools. A Black Belt should demonstrate team leadership, understand team dynamics, and assign team member roles and responsibilities. Black Belts have a thorough understanding of all aspects of the DMAIC model in accordance with Six Sigma principles. They have basic knowledge of lean enterprise concepts, are able to identify nonvalue-added elements and activities, and are able to use specific tools.
What are core competencies of a Lean Six Sigma Black Belt?
✅ Black Belts have a thorough understanding of all aspects of the define, measure, analyze, improve, and control (DMAIC) model in accordance with Six Sigma principles.
✅ They have basic knowledge of lean enterprise concepts, are able to identify nonvalue-added elements and activities, and are able to use specific tools.
✅ Advanced understanding of project definition as well as team roles and responsibilities.
✅ Advanced understanding of the measure phase, including process mapping, data collection plans and techniques, understanding variation, and visually displaying baseline performance.
✅ Advanced understanding of the analyze phase, including displaying data visually, cause and effect analysis, and verification of root causes.
✅ Advanced learning of the improve phase, including brain-storming, selecting a solution, and implementation planning.
✅ Advanced understanding of the control phase, including assessing the results of process improvement, statistical process control overview, and documenting the process.
Target Participants
Professionals who are working as Executive, Administrator, Auditor, Consultant, Engineer, Analyst, Inspector, Manager, Project Manager, Quality Analyst, Senior Leve employees, Supervisors, team Leaders and the likes working in the Education, Energy, Government, Healthcare, Information Technology, Manufacturing, Medical Device, Military, Pharmaceutical, Service, Transportation and virtually all industries.
Program Outline (based on Council for Six Sigma Certification (CSSC), American Society for Quality (ASQ) and curated best practices and published successful projects
Define Phase
1.1 Six Sigma Overview
1.1.1 What is Six Sigma
1.1.2 Six Sigma History
1.1.3 Six Sigma Approach Y = f(x)
1.1.4 Six Sigma Methodology
1.1.5 Roles and Responsibilities
1.2 Six Sigma Fundamentals
1.2.1 Defining a Process
1.2.2 VOC and CTQs
1.2.3 QFD
1.2.4 Cost of Poor Quality (COPQ)
1.2.5 Pareto Analysis (80 : 20 rule)
1.3 Lean Six Sigma Projects
1.3.1 Six Sigma Metrics
1.3.2 Business Case and Charter
1.3.3 Project Team Selection
1.3.4 Project Risk Management
1.3.5 Project Planning
1.4 Lean Fundamentals
1.4.1 Lean and Six Sigma
1.4.2 History of Lean
1.4.3 The Eight Wastes
1.4.4 Five-S (5S)
Measure Phase
2.1 Process Definition
2.1.1 Cause and Effect Diagrams
2.1.2 Cause and Effects Matrix
2.1.3 Process Mapping
2.1.4 FMEA: Failure Modes & Effects Analysis
2.1.5 Theory of Constraints
2.2 Six Sigma Statistics
2.2.1 Basic Statistics
2.2.2 Descriptive Statistics
2.2.3 Distributions and Normality
2.2.4 Graphical Analysis
2.3 Measurement System Analysis
2.3.1 Precision and Accuracy
2.3.2 Bias, Linearity, and Stability
2.3.3 Gage R&R
2.3.4 Variable and Attribute MSA
2.4 Process Capability
2.4.1 Capability Analysis
2.4.2 Concept of Stability
2.4.3 Attribute and Discrete Capability
2.4.4 Monitoring Techniques
Analyze Phase
3.1 Patterns of Variation
3.1.1 Multi-Vari Analysis
3.1.2 Classes of Distributions
3.2 Inferential Statistics
3.2.1 Understanding Inference
3.2.2 Sampling Techniques and Uses
3.2.3 Sample Size
3.2.4 Central Limit Theorem
3.3 Hypothesis Testing
3.3.1 Goals of Hypothesis Testing
3.3.2 Statistical Significance
3.3.3 Risk; Alpha and Beta
3.3.4 Types of Hypothesis Tests
3.4 Hypothesis Testing: Normal Data
3.4.1 One and Two Sample T-Tests
3.4.2 One sample variance
3.4.3 One Way ANOVA
3.5 Hypothesis Testing: Non-Normal Data
3.5.1 Mann-Whitney
3.5.2 Kruskal-Wallis
3.5.3 Moods Median
3.5.4 Friedman
3.5.5 One Sample Sign
3.5.6 One Sample Wilcoxon
3.5.7 One and Two Sample Proportion
3.5.8 Chi-Squared (Contingency Tables)
3.5.9 Test of Equal Variances
Improve Phase
4.1 Simple Linear Regression
4.1.1 Correlation
4.1.2 X-Y Diagram
4.1.3 Regression Equations
4.1.4 Residuals Analysis
4.2 Multiple Regression Analysis
4.2.1 Non-Linear Regression
4.2.2 Multiple Linear Regression
4.2.3 Confidence Intervals
4.2.4 Residuals Analysis
4.2.5 Data Transformation, Box Cox
4.2.6 Stepwise Regression
4.2.7 Logistic Regression
4.3 Designed Experiments
4.3.1 Experiment Objectives
4.3.2 Experimental Methods
4.3.3 DOE Design Considerations
4.4 Full Factorial Experiments
4.4.1 2k Full Factorial Designs
4.4.2 Linear and Quadratic Models
4.4.3 Balanced and Orthogonal Designs
4.4.4 Fit, Model, and Center Points
4.5 Fractional Factorial Experiments
4.5.1 Designs
4.5.2 Confounding Effects
4.5.3 Experimental Resolution
Control Phase
5.1 Lean Controls
5.1.1 Control Methods for 5S
5.1.2 Kanban
5.1.3 Poka-Yoke (Mistake Proofing)
5.2 Statistical Process Control (SPC)
5.2.1 Data Collection for SPC
5.2.2 I-MR Chart
5.2.3 Xbar-R Chart
5.2.4 U Chart
5.2.5 P Chart
5.2.6 NP Chart
5.2.7 X-S chart
5.2.8 CumSum Chart
5.2.9 EWMA Chart
5.2.10 Control Methods
5.2.11 Control Chart Anatomy
5.2.12 Subgroups, Variation, Sampling
5.3 Six Sigma Control Plans
5.3.1 Cost Benefit Analysis
5.3.2 Elements of the Control Plan
5.3.3 Elements of the Response Plan
An enriching journey for better process improvement.
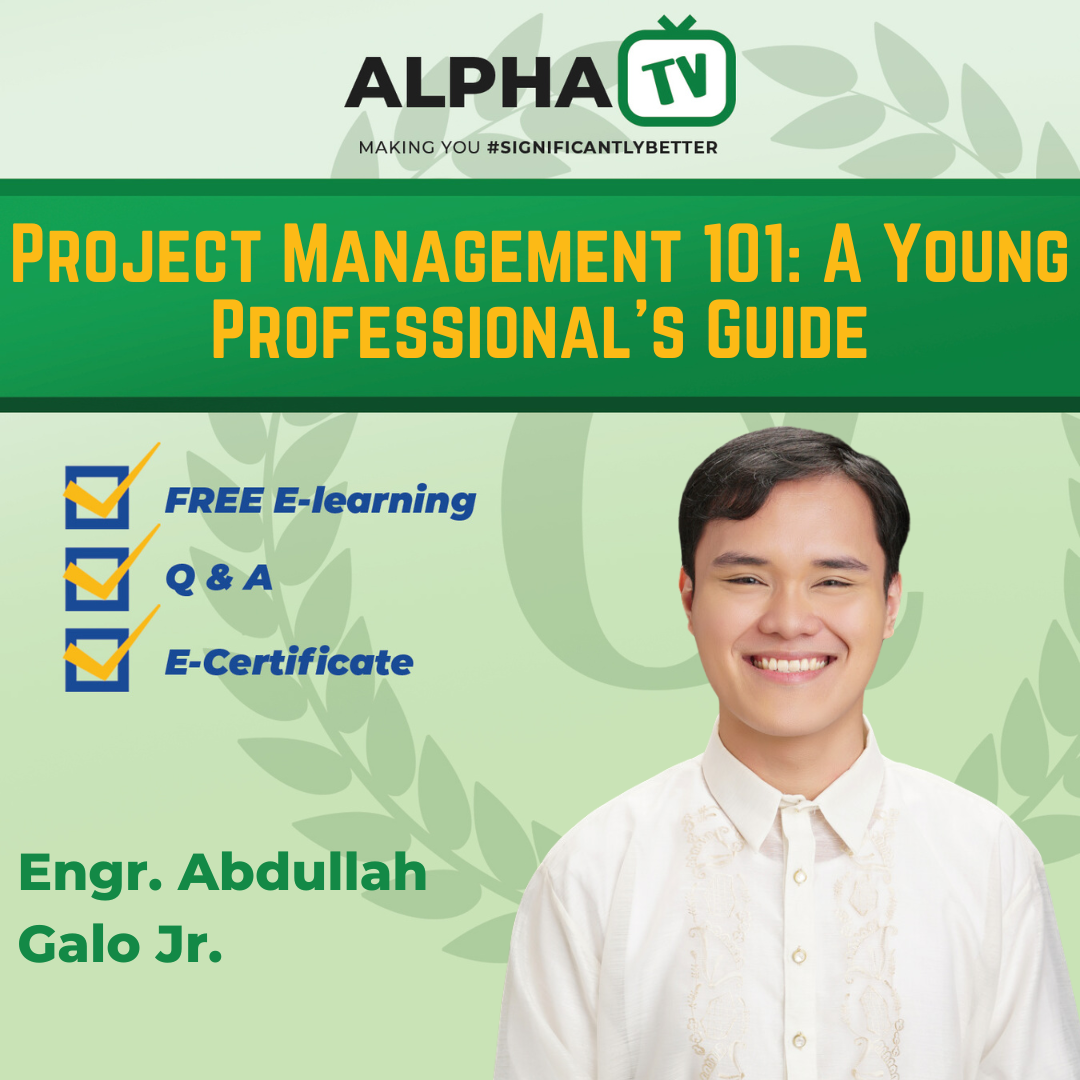
AG
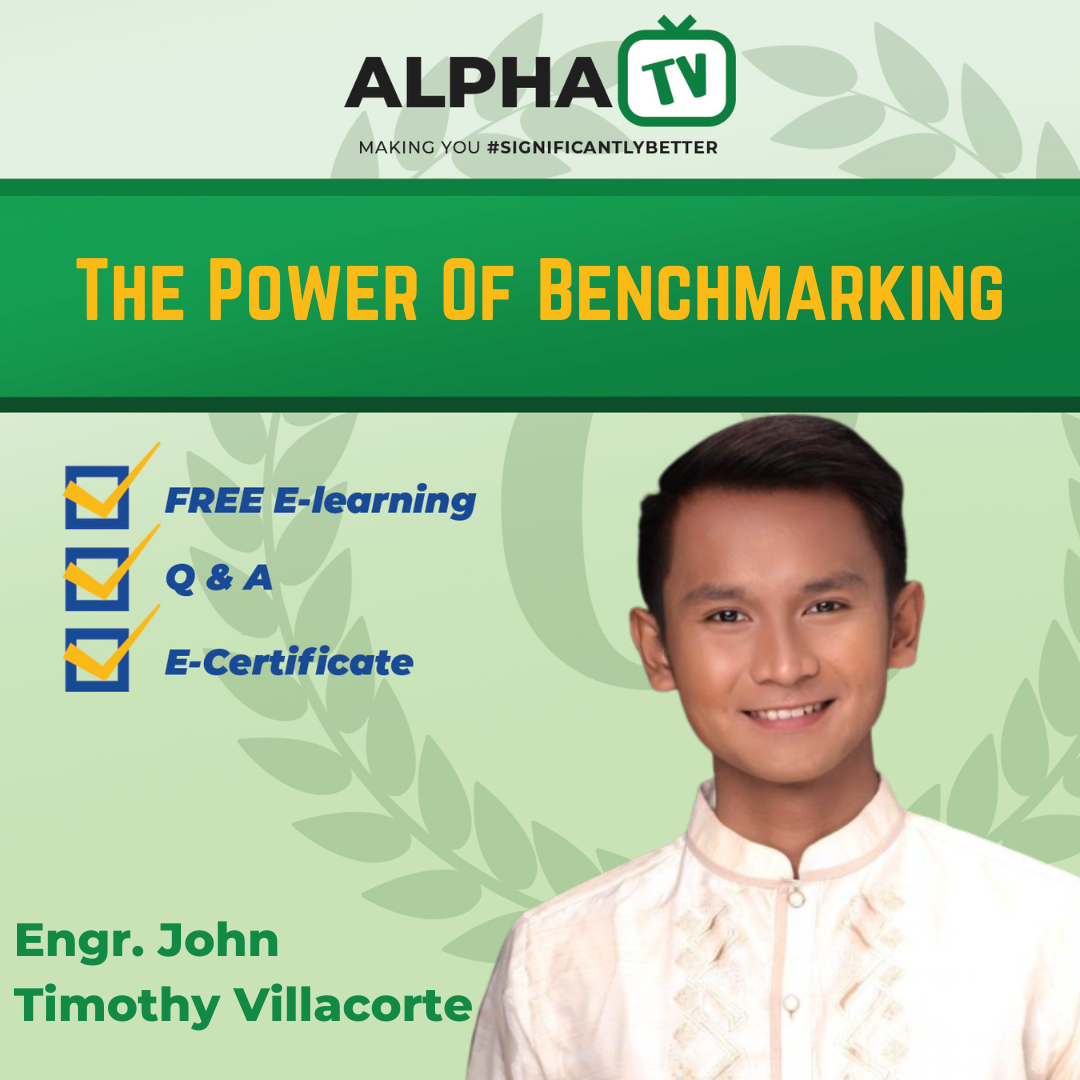
JV
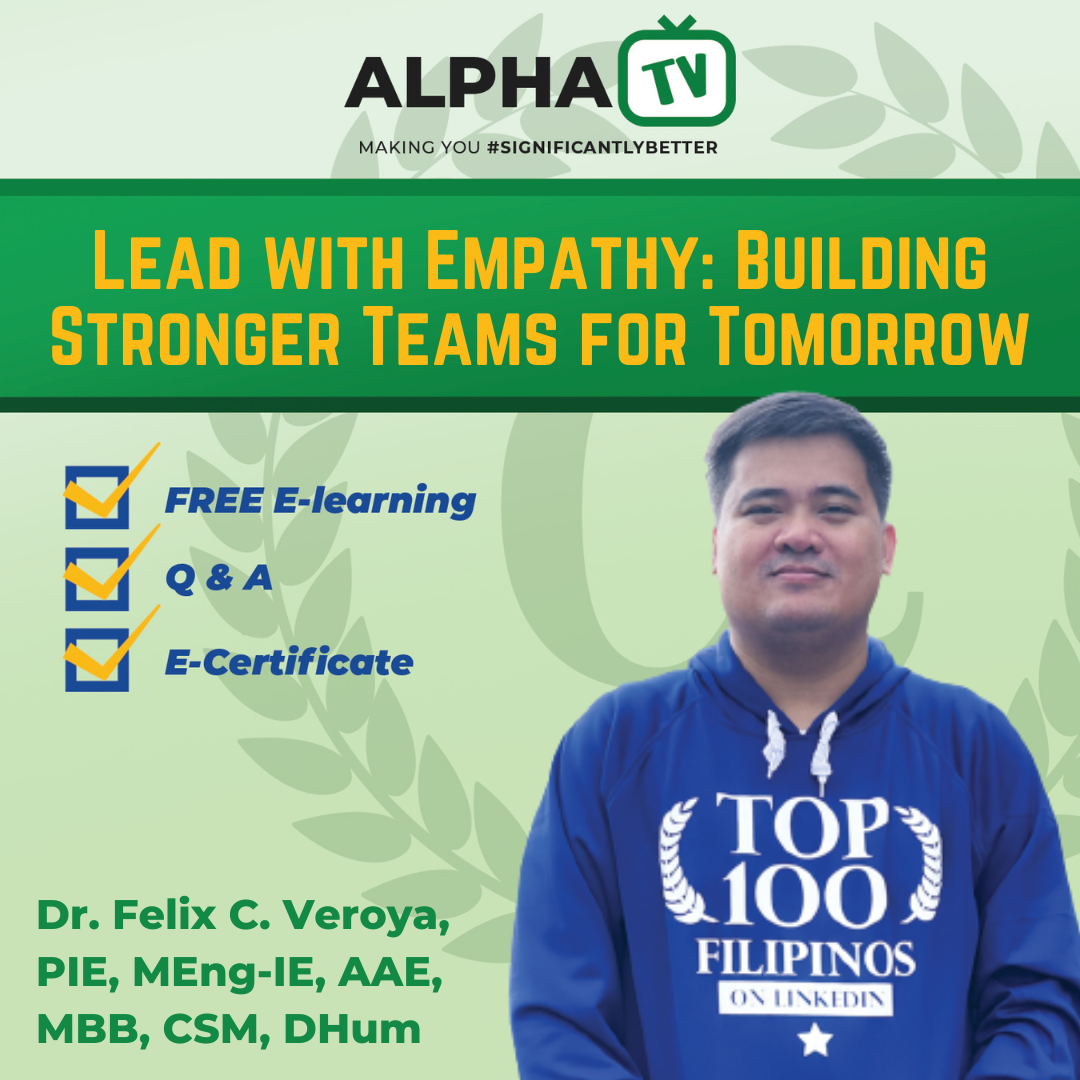
FV